The Art Behind Barichara's All-Female Artisanal Paper Making
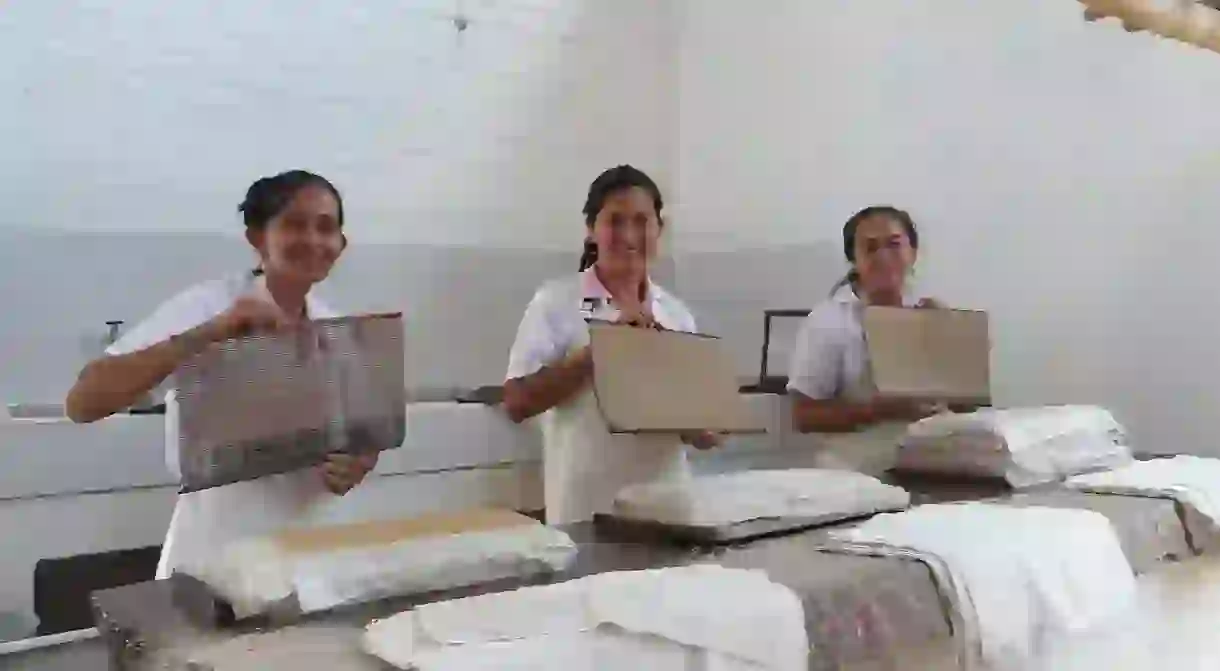
Created in 2001 with the aim of financially supporting single-parent women, Fundación San Lorenzo‘s paper-making factory is today the number one employer in Barichara – and a lifeline for women in search of a job. In a town where work is scarce and opportunities few, the four-month-long process of making paper from fique – a natural fiber that grows in the leaves of the Andean fique plant – has become the vital organ of Barichara’s female working community. Read on for a glimpse into what it takes to make these precious sheets from nothing but natural resources, an old tobacco press, and the willpower of 11 women.
Step 1: Extracting the fiber from the plant
The cactus-like Andean fique plant grows in warm, tropical climates and can be found in Colombia, Peru and Ecuador. The long, prickly leaves are collected by the women in the neighbouring fields using big weaved baskets. Back at the factory, the leaves are put through an extractor machine by hand to separate the skin from the fibers. The skin is discarded, and what is left are thousands of fine but tough white fibers. This wispy, hair-like material will form the base of every sheet of paper made here.

Step 2: Cooking the fique over an open fire
Before the fique fiber can be used to make paper, it must be softened. To do this, the strands are first soaked in calcium oxide and then coated in a gelatine and ash paste and cooked in large copper containers over a high flame. Once the fique fibers have softened, they are removed from the heat and rinsed through with cold water.

Step 3: Bashing the fique by hand
Now the hard work starts. Once the fique has been rinsed through, it is taken over to the “machacada” (meaning “bashing”) station, a centuries-old technique used to beat the moisture out of the fique. Using a wooden baton, the women bash the fique flat. Eventually, the fibers fuse together into a sticky, square-sized pulp.
Step 4: Shaping and dyeing the paper
The pulp is now transferred to the sinks, where it is placed in a mesh/wooden frame to make the classic A4 sized sheet. If the sheet is to be coloured, natural dye is added to the water at this stage. The sheet is then placed on a piece of canvas ready for pressing and drying.

Step 5: Removing excess water
To remove the excess water, the sheet of paper is placed under the wooden press, which has to be hand-turned by the women using a huge steel wheel. The press is more than a century old; it was left behind on the property from Barichara’s tobacco-making heyday (the press then would’ve been used to flatten the tobacco leaves).

Step 6: Drying
Once every drop of water has been squeezed out, the sheets are hung up in the factory to dry naturally, filling the entire room with hundreds of fique sheets, which will later be sold (both as plain sheets and hand-made paper gifts and stationary) in the factory’s small shop.

Step 7: The final press
Once the sheets are completely dry, it’s time for the last step. To produce a crisp, perfectly flat sheet, the paper must go under a weighted press for several hours. The ladies here say that the longer you leave a sheet in the press, the more beautiful the paper will turn out. A metal sheet is placed between each piece of paper and left to flatten. The result? Beautiful artisanal paper made from 100% natural materials – and without the use of a single piece of modern machinery.

The Fundación San Lorenzo de Barichara has even begun to experiment with other materials such as pineapple, marijuana, tobacco and banana leaves in order to boost their production volumes and continue growing the organisation. If you’re in town, make sure you stop by to make your very own fique sheet, all while supporting the women of Barichara.